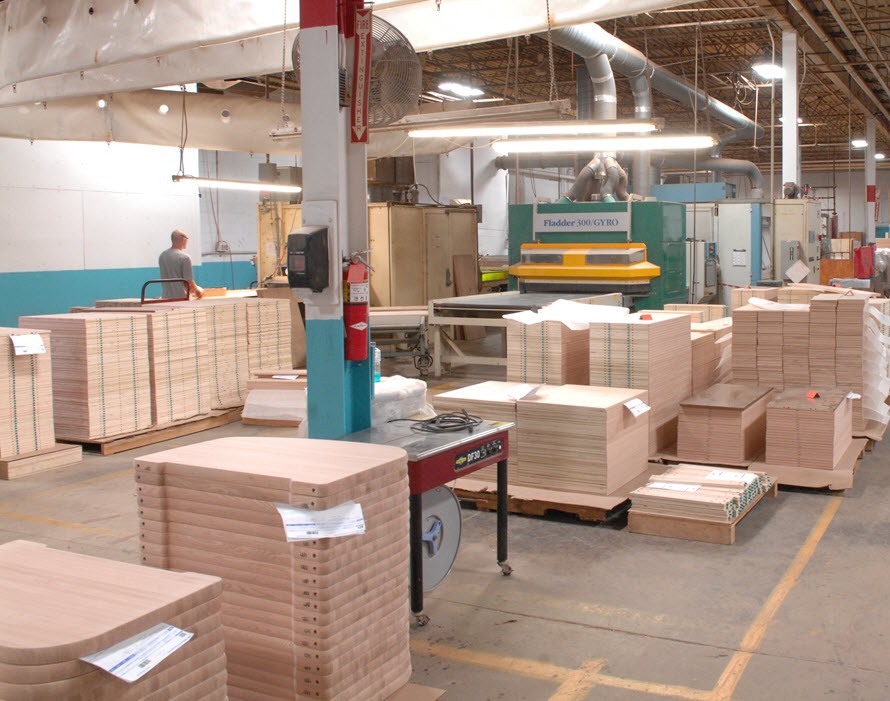
Each of our processes is unique, significant, and value-adding to your furniture.
UV Cured Resin | Flat Line Technology
Our wood furniture is sealed and top coated using Moduform’s industry-leading, specially formulated, UV cured resin. This finish is rich looking, extremely durable, and is permanently bonded to the wood.
UV resin is easy to clean and maintain and will withstand heavy-use detergents as its non-reactive chemistry and other distinctive characteristics enable it to hold up to the rigors and unpredictable circumstances that arise in your facility. Moduform applies the resin using through feed, flat line roll coating applicators.
With our process, there are no solvents to evaporate, no environmental pollutants, no loss of coating thickness, and no loss of volume, all of the material is simply rolled onto the part and dried under high-intensity UV lamps. The environmental benefits alone make the Moduform process second to none. The superior physical properties only add to the exceptional value. It’s resistant against ever day abrasion from books, papers, and writing instruments. It repels most food and beverage stains, prevents discoloration from strong light and temperature variation, and is tough enough to withstand bleach-based cleaners and heavy strength disinfectants…even nail polish remover!
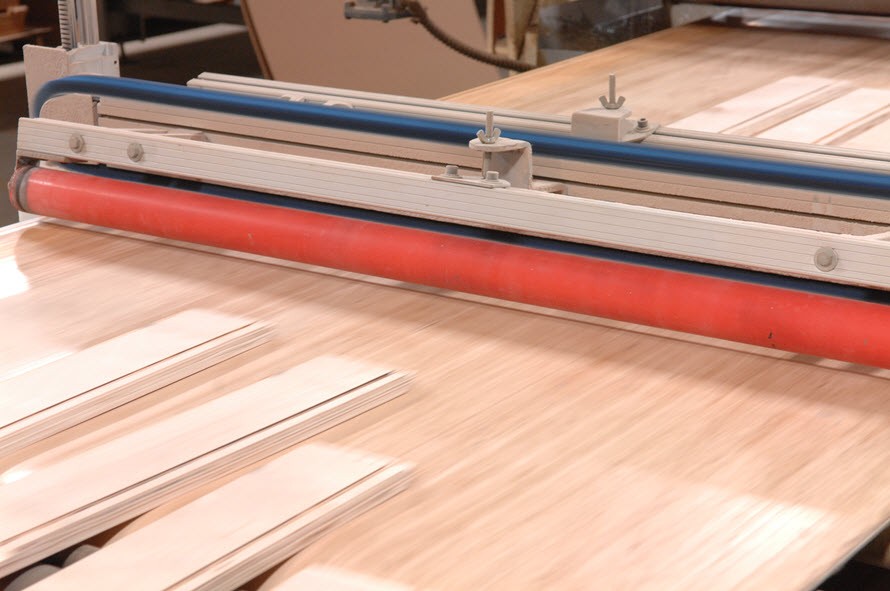
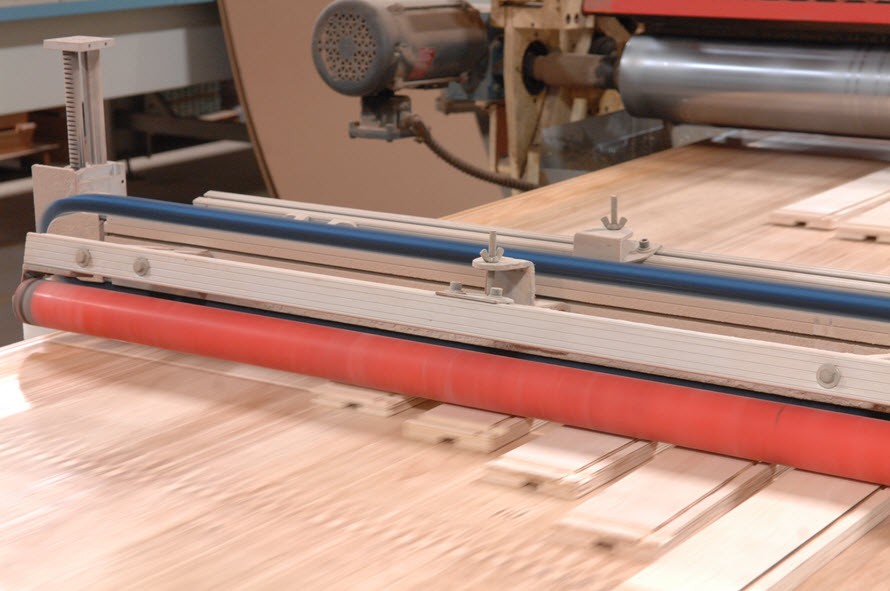
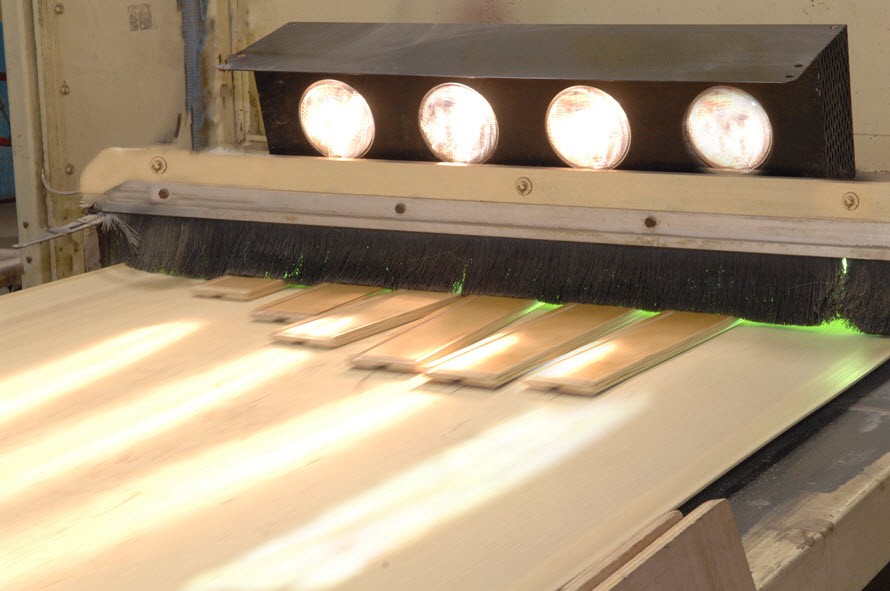
Spray Line Wood Finish
Before we topcoat wood components with our UV cured resin, all products specified for one of our four (4) standard finishes or custom color undergo a computer-controlled staining operation. All Moduform finishes are specially formulated and water-based so that they are environmentally friendly, true to color, and consistent. Material is precisely calculated and any over-spray is captured and re-used. The consistency of the color is unmatched and the quality of the product is second to none.
Here’s a little video that shows how our spray-stain process works:
Rotational Molding (Rotomolding)
Moduform has been rotomolding lounge seating and cushions and other furniture components since its inception in 1976. The process requires large, industrial molds to form components and complicated, large-scale ovens and cooling chambers to ensure parts are uniform in thickness, well-shaped, and meet the standard necessary for continual use in unpredictable settings.
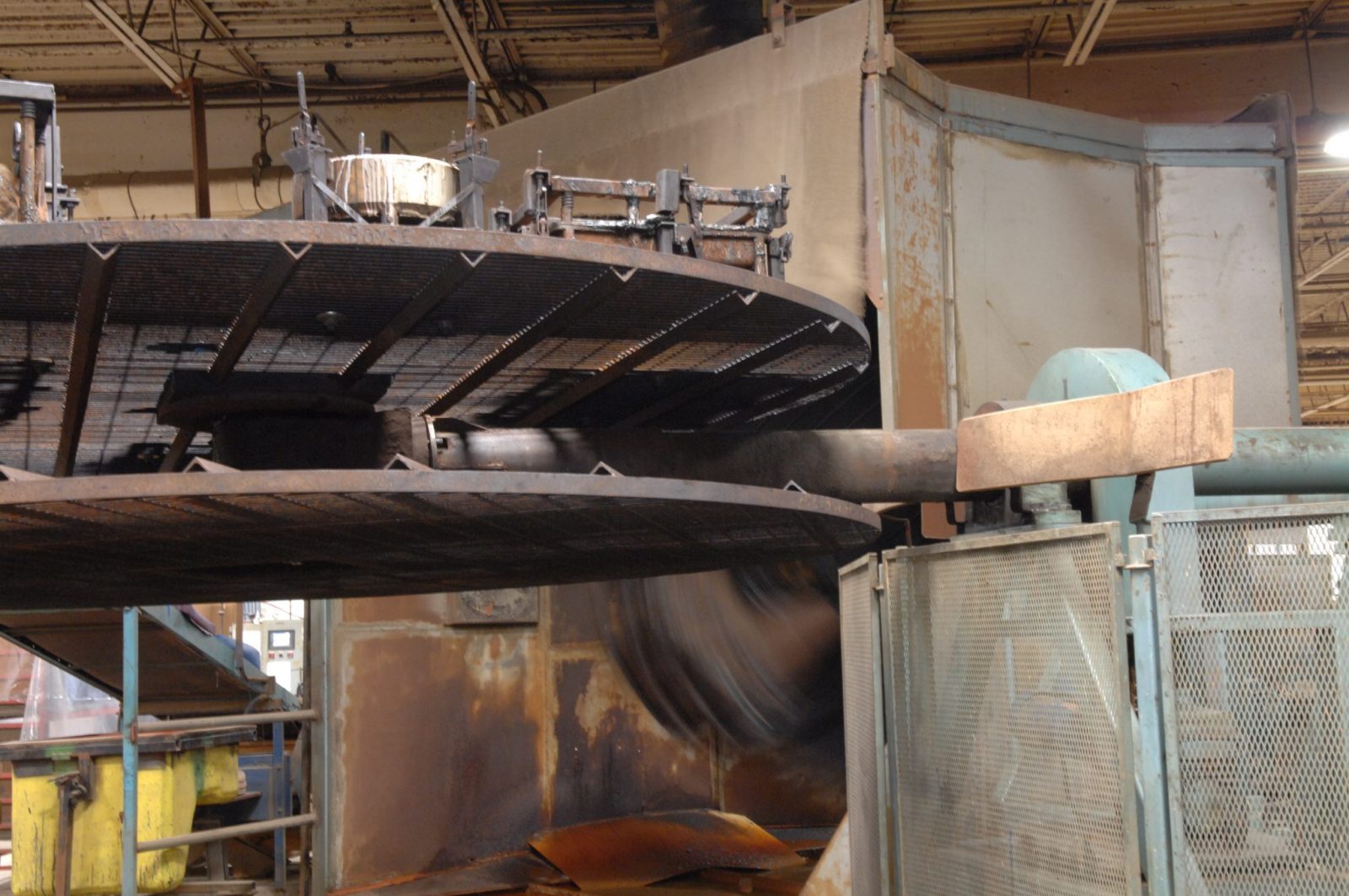
Moduform has the unique capability to manufacture products with two different materials. Polyvinyl chloride is used in the production of our soft, foam-filled 520 series lounge seating, 450 Series Seclusion Beds and cushions for 3000 series beam seating and 350, 600, 800, and 810 collections of wood-sided lounge. Linear, Low-Density Polyethylene is used when we are producing rigid plastic parts as can be found in 5000-250 ModuMaxx lounge, 5000 Series X-Base tables, and 5000 series beam seats. While the process is nearly identical for both materials, the type of product produced is quite different. Both yield seamless, fluid, and pick resistant pieces that are very easily cleaned. However, the Polyvinyl Chloride units are filled with a high-density polyurethane foam that is fused to the inside skin of the piece. This produces a soft, comfortable, and secure product that meets Life Safety codes will withstand the rigors of daily use in critical environments and is comfortable. Polyethylene pieces are rigid in shape, hollow at the core, and can be ballasted to add weight when necessary.
The process begins with securing heavy-duty molds to large plates. Pre-determined quantities of raw material are then dispensed into the molds. The plates, which are mechanically fastened to rotating arms, are then set into a spinning and tumbling motion at low rates of speed. This allows for material in the molds to form into a uniform thickness and shape. Whether we are using Polyvinyl or Polyethylene, heat solidifies the profile and cures the material. Cooling chambers are in line so that parts can be removed from molds at the appropriate temperature for final assembly or foam filling.
All Polyvinyl units are filled with Moduform’s specially formulated, high-density polyurethane foam. Our filling material is durable, flexible, and solidifies as one piece. This makes it the longest-lasting in the industry. We use high-pressure mixing heads to dispense material into the molded cavity allowing it to securely bond to the inside skin face. The end result is a soft, durable, and comfortable lounge piece or cushion that will meet the needs of uncompromising environments for many years.
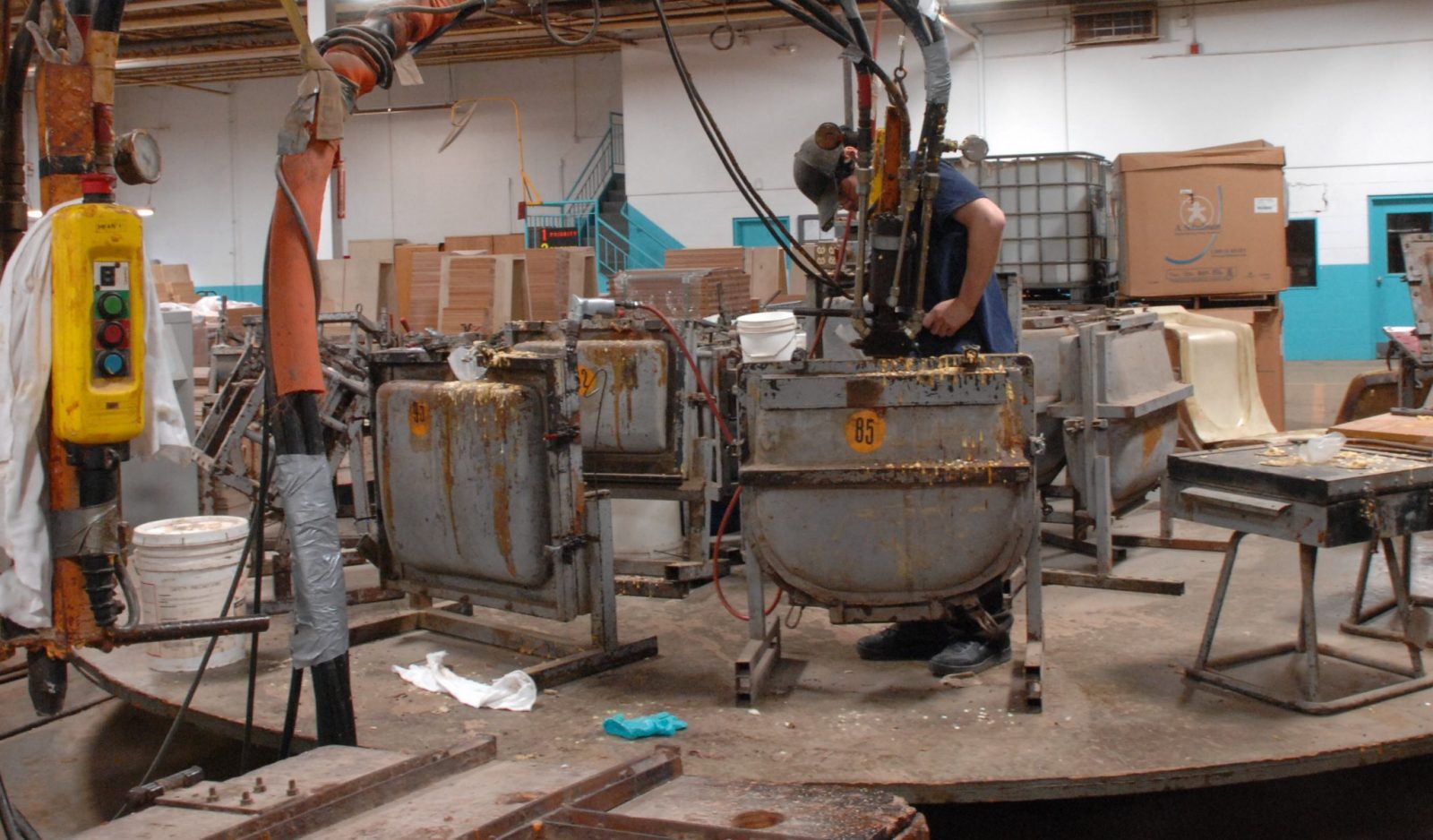
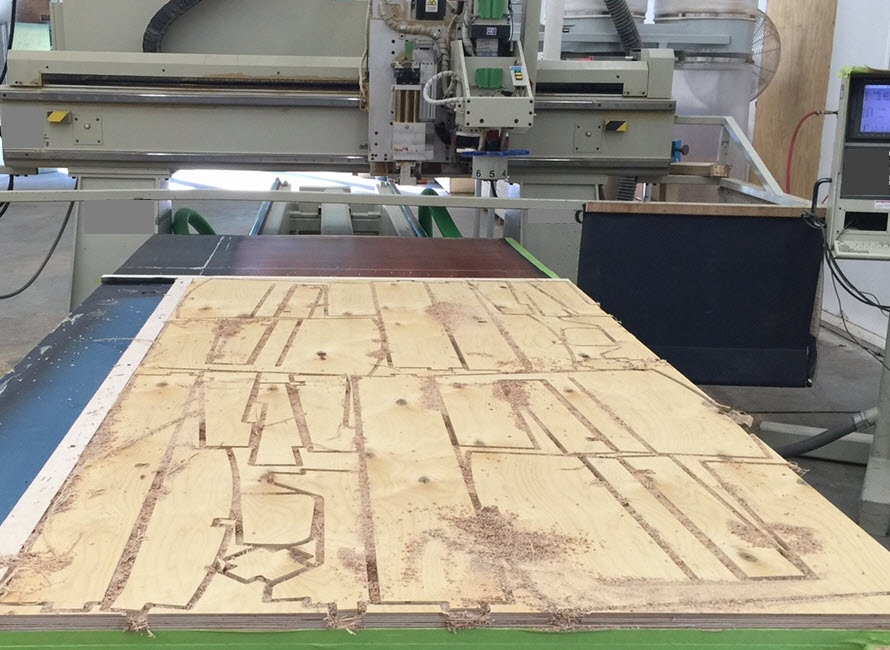
Puzzle Cutting
Moduform manufactures durable, attractive, and contemporary fully upholstered lounge seating. Our Connelly Springs, NC factory fabricates frame components using heavy-duty sheets of plywood to the tightest of tolerances. Our process begins by loading a sheet of plywood on to a state of the art, nested base, computer-controlled router. The table and gantry guide the cutting tool, first, by plunging a router bit into the material and then, machining all the component parts into “puzzle” like shapes.
After the pieces are removed from the “nest”, our frame assemblers interlock each member; much like the traditional and time-tested mortise and tenon joint. We further support each area with industrial glues and mechanical fasteners. After frames have been completed, we connect heavy gauge springs, reinforce them with paper-covered tie rods for “no-sag” construction and affix them engineered hardwood rails using tape lined clips to prevent squeaking. All inner hardware is concealed and softened using cover and densified batting. Fabric is cut, sewn (using an appropriate stitch), and upholstered to the piece with fine detail. The tailoring of the final unit is exemplified with the four-way match to ensure fit and finish meets our tight quality standards.
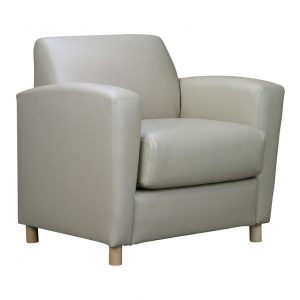
Flex Cover
Moduform upholstery frames are so durable, recovering components should be taken into consideration when investing in our furniture; our frames last a long time! With our unique “Flex Cover” design, hook and loop fastening is used so that covers are easily replaced without the need for tools or the knowledge of upholstering. Covers can be removed in minutes and new ones can be slipped on quickly. Moduform takes great pride in the fit and finish of the final piece. A “Flex Cover” model is indecipherable from a traditional upholstered piece.
Newsletter
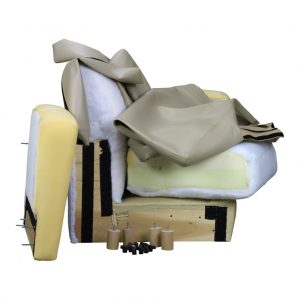